Producing industrial ethanol requires careful attention to detail and a thorough understanding of the fermentation process. Optimal ethanol fermentation can be achieved through various optimization factors: choice of the yeast, fine tuning of process parameters, contamination control, and so on.
1. Selecting the right yeast strain
Different yeast strains have different abilities to ferment various types of feedstocks. It is important to choose a yeast strain that is adapted to the raw materials – corn, sugar beet, cassava, rice, sugarcane, lignocellulose, etc. – , the geography, and the process of an ethanol plant. This is one first step that has a major impact on the industrial ethanol production process.
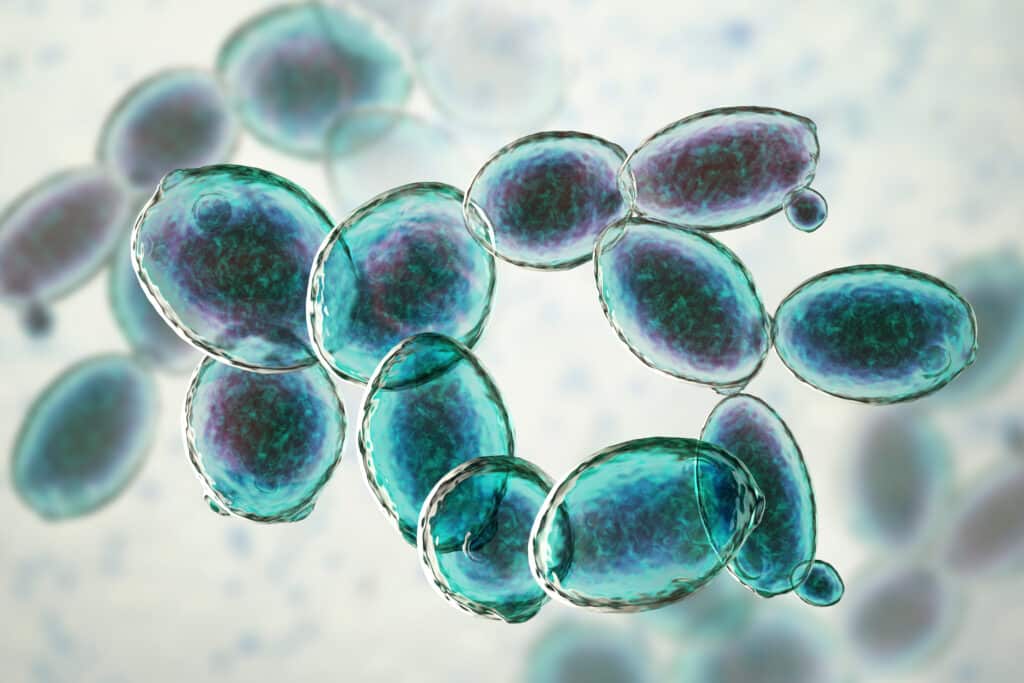
2. Mastering rehydration
With the use of dry yeast, a suitable rehydration is essential for optimal ethanol fermentation. Underestimating the rehydration step is taking the risk to decrease yeast cells viability, and thus end up with incomplete fermentations. Yeast should be rehydrated in 5 to 10 times its volume of water: 100kg (220lbs) of yeast should be rehydrated in 500kg to 1 tonne (1.1k to 2.2k lbs) of water. Temperature must also be carefully controlled to be around 35°C±5 (around 95°F) during rehydration, to preserve yeast membranes. A gentle stirring for 15-30 min is also recommended.
3. Optimizing propagation to reach optimal ethanol fermentation
Propagation conditions should allow a maximum amount of yeast to be produced, to ensure optimal ethanol fermentation performances once pitched. To reach the right quantity and quality of yeast the exponential growth phase, the pitching rate should be between 0.25kg and 1kg of yeast par cubic meter of propagator (depending on the yeast strain and the process) and the growth should be exponential (to ensure non limited growth). The goal here would be to reach at least 250 million yeast per mL in exponential phase.
4. Setting up the proper environment for optimal ethanol fermentation
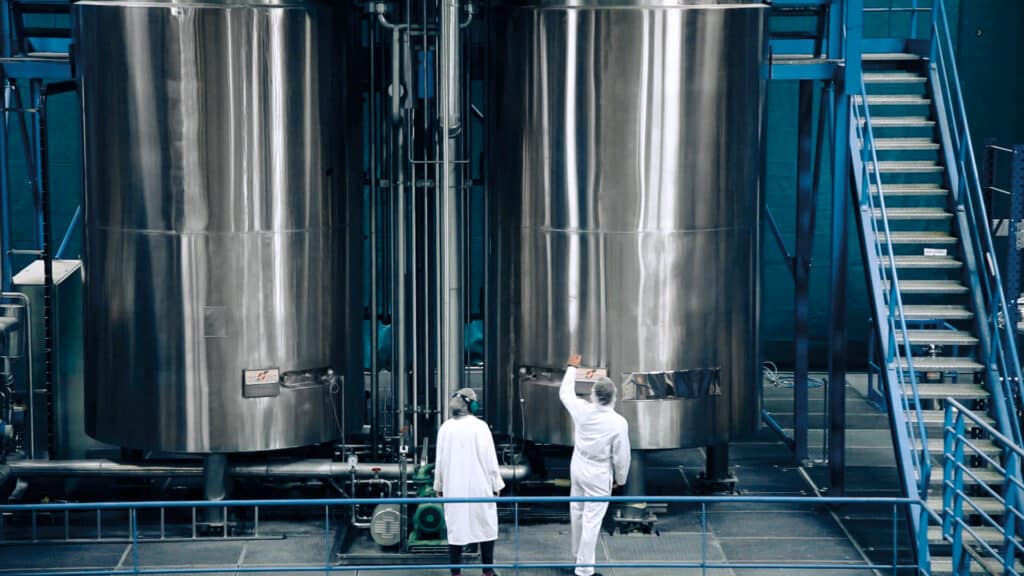
Performing optimal ethanol fermentation goes through providing the yeast with the right environment to ferment sugars. Different parameters can be optimized to avoid fermentation stress:
- Maintaining a consistent and ideal temperature throughout the fermentation process, between 30 and 35°C – going up to 40°C with the right robustness of the yeast.
- Optimizing the pH – between 4.0 to 5.5. Working with a pH in the high side of range contributes to decrease the toxicity of acetic acid, as in the case of substrates rich in acetic acid (which pKa is 4.76). It can be applied when contamination is under control because the higher the pH is, the more bacteria can grow.
The case of very high temperatures in India
Indian summers can get very hot, hotter than the recommended temperatures for fermentation processes. Managing fermentation under higher temperatures is even more difficult because it is a crucial parameter. Various parameters can be optimized to maintain ideal temperatures throughout the fermentation process, such as:
- Maintaining cooling towers efficiency, by ensuring equipment is in good operating conditions and by supplying cold water into them
- Investing in chillers, to maintains optimal temperatures and counteracts heat from the fermenting yeast & surrounding climate
- Adjusting the level of nitrogen supplementation and its dosing time during fermentation, to limit metabolic heat of the yeast
5. Ensuring proper yeast nutrition
Yeasts require a variety of nutrients in order to grow and efficiently ferment feedstocks: nitrogen, phosphorus, vitamins, and minerals. It is important to provide the proper ratio of bioavailable nutrients to ensure that the yeast can grow and ferment efficiently. Nutrition deficiencies can result in lower yields, slower fermentation rates, or even incomplete fermentations.
6. Preventing biological stress from contamination
Contamination can happen during fermentation, causing biological stress to the yeasts. Minimizing contamination with a smart choice of process parameters – pH, temperature, etc. – will decrease the bacteria growth rate. Another manner of reducing contamination goes through maintaining a clean and sanitary fermentation environment. Performing optimal cleaning in place (CIP), properly sterilizing equipment and fermenters, and using proper hygiene practices is the most efficient way of minimizing contaminations.
7. Targeting high gravity
Targeting the highest ethanol titer, through high gravity fermentation minimizes water consumption, CO2 emissions and energy costs at distillation, increasing ethanol fermentation’s economic viability. Carrying out high gravity fermentations requires, among other conditions, an optimized propagation and faster yeast kinetics.
The case of SSF processes
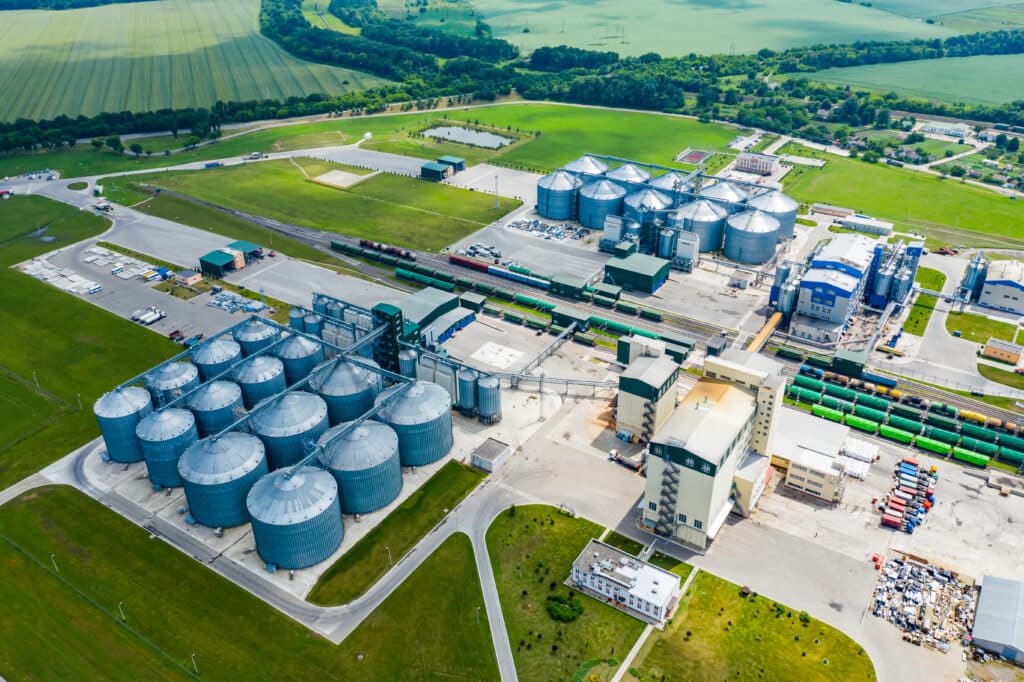
In the case of simultaneous saccharification & fermentation (SSF) processes, releasing too much or not enough sugar can either limit yeast kinetics or increase osmotic pressure; resulting in both cases in low ethanol production performance. Fine tuning enzyme addition, and well as ensuring a good match between hydrolysis kinetics and yeast kinetics will allow optimal ethanol productivity and yield.
How does our plant performance assessment support in India helps our partners to perform optimal ethanol fermentations and maximize their profitability?
In India, our local technical team assesses our partner’s plant performances through data collection: how much industrial ethanol is produced per day (KLPD), total fermentation cycle time, pre-fermenter to fermenter ratio, yeast dosing, gravity, etc. Our market knowledge and expertise at local scale enables us to identify bottlenecks, preventing our partners to perform optimal ethanol fermentations.
The team harnesses important information through data-mining and specific statistical tools to identify the tracks of improvements.
To address the identified issues, we provide tailor-made technical programs. We then support implementation of the solutions through teamwork with the customer solution team & production section. This support can go from optimizing propagation, via maximizing specific growth-rate of the yeast, to improving supplied air quality, limiting fermentation stresses, and many other parameters optimization.
Overall, performing the most optimal ethanol fermentation is important for maximizing efficiency, yield, and quality while minimizing environmental impact. This happens when carefully considering the variety of factors cited above. Taking into account the whole production process and performing all necessary adjustments when producing industrial ethanol limits yeast stresses and favorizes consistent and efficient fermentations, thus improving plant profitability.